Maintaining the integrity and appearance of concrete surfaces is a common concern in both residential and commercial settings. Concrete patch is an essential product used for repairing cracks and holes that inevitably develop over time. These patches help restore the structural strength and aesthetic appeal of concrete floors, sidewalks, steps, and other surfaces. The process involves filling in defects with a blend of materials that bond to the existing concrete and cure to form a durable repair.
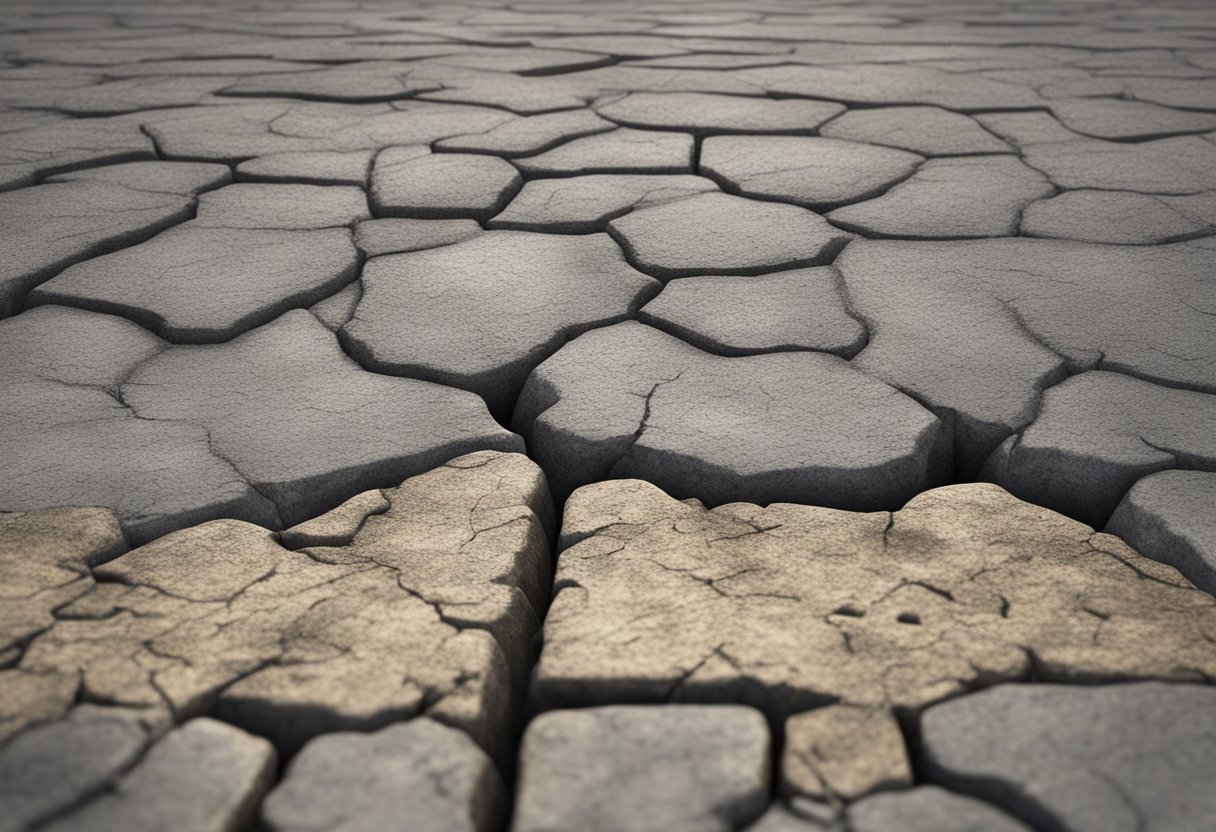
Selecting the right concrete patch material is crucial for ensuring a lasting repair. There are various types available on the market, each tailored for different types of damage and concrete surfaces. For instance, a vinyl concrete patcher provides a strong adhesive bond and is easy to apply, making it suitable for smooth repairs to small cracks and chips. Understanding the pros and cons of each option helps individuals make an informed decision on which product is best suited for their repair needs.
The application process is equally important to the success of a concrete repair. It typically involves preparing the damaged area, mixing the patching compound, and applying it correctly. Detailed instructions, such as those provided by How to Repair Cracked Concrete, guide users through methods for addressing various forms of concrete damage. With proper technique and curing time, these patches can extend the life of concrete surfaces significantly, saving time and money on potential future repairs.
Understanding Concrete and Repair Materials
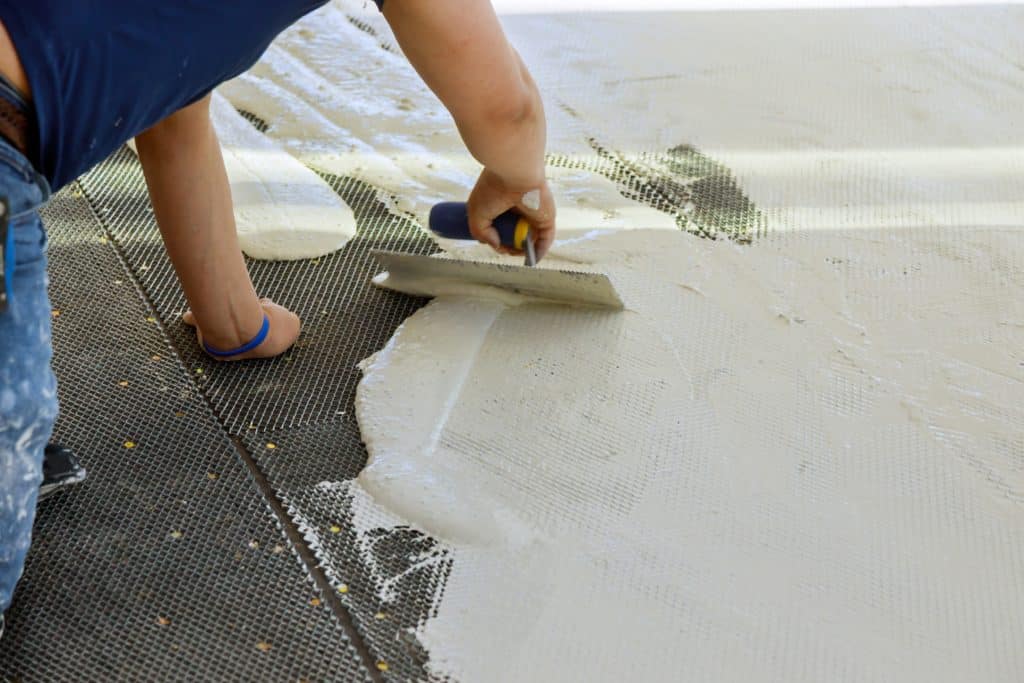
In the realm of building and construction, the longevity and integrity of concrete structures is paramount. This section delves into the composition of concrete patching compounds and the strategic selection of additives to enhance durability.
Types of Concrete Patching Compounds
Concrete patching compounds are vital for restoring the structural soundness and surface uniformity of damaged concrete. They come in various forms to cater to different repair needs:
- Epoxy Patching Compound: Highly valued in industrial and commercial applications due to its superior strength and bonding properties.
- Vinyl Concrete Patch: Composed of vinyl resins that offer flexibility and adhesion, making it suitable for small to moderate repairs on concrete surfaces.
- Hydraulic Cement: Known for its rapid setting time and water resistance, hydraulic cement is used in areas where quick turnaround and moisture exposure are concerns.
- Quikrete: A popular ready-to-use mixture that only requires water, providing convenience and quality for concrete repairs.
Selecting the Right Additives for Durability
To ensure the repaired concrete can withstand environmental stress and time, the correct choice of additives is critical:
- Epoxy: When added, it dramatically increases the material’s resistance to chemicals and physical impact, making it ideal for floors and heavy-load areas.
- Acrylic: Acrylic additives enhance the bonding to the existing concrete and provide better weathering properties.
- Vinyl: Including vinyl enhances the product’s flexibility and tensile strength, which helps to prevent future cracks.
- Additives: Specific additives can be incorporated to accelerate or decelerate the setting time, improve workability, or reduce shrinkage.
Selecting the appropriate compound and additive mix can significantly extend the life of concrete repairs, providing both resilience and durability.
Surface Preparation and Application Techniques
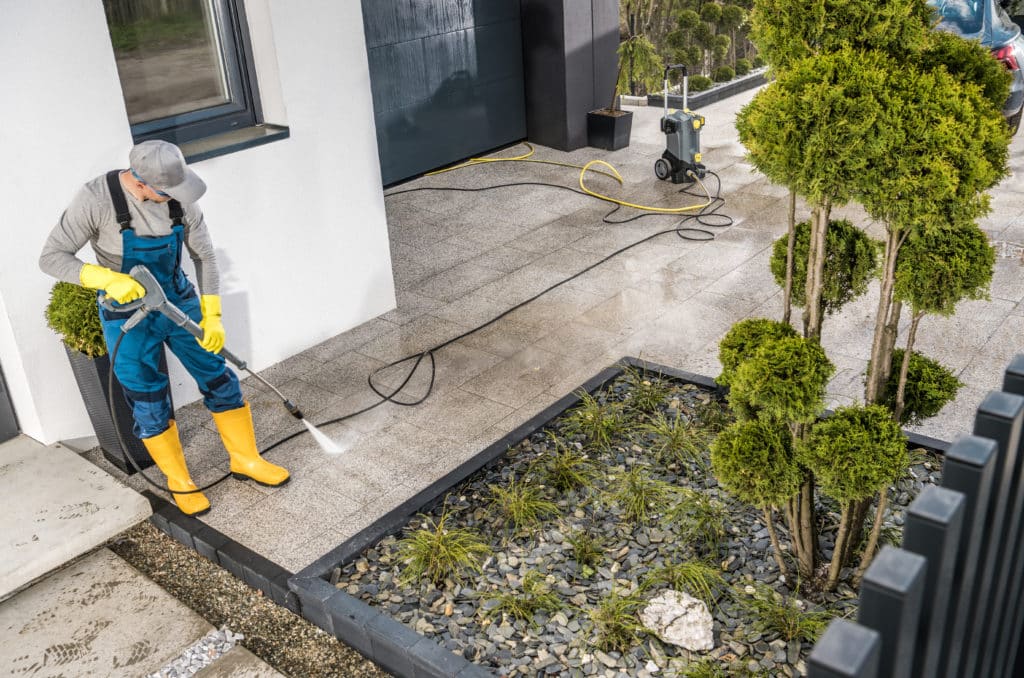
Proper surface preparation and application are critical for ensuring durable repairs on concrete floors, driveways, sidewalks, and masonry surfaces. This section focuses on the steps required to prepare surfaces and the best practices to apply patching compounds effectively.
Cleaning and Priming Concrete Surfaces
Cleaning: The longevity of a repair is highly dependent on the cleanliness of the concrete surface. All contaminants—oils, dirt, or loose particles—must be rigorously removed to ensure a strong bond between the patching compound and the concrete. Methods used may include power washing, shot blasting, or chemical cleaning.
Priming: Once the surface is clean, priming is often the next step for surfaces not receiving a polymer bonding agent. A primed surface ensures an optimal bonding environment for the patching compound. This step is essential especially for surfaces with heavy foot traffic, such as sidewalks or garage floors.
Applying Patching Compounds for Optimal Bonding
- Material Selection: Choosing the right patching compound is crucial. For example, a polymer-modified cementitious compound may be preferred for its ease of application and flexibility.
- Application: Uniform application of the patching compound is necessary for a strong bond and to prevent future failures. It’s important to apply it according to the manufacturer’s guidelines to achieve the best results for concrete floors, driveways, and other surfaces.
The final quality of a concrete patch is significantly affected by these preparation and application techniques. They are not just recommendations but essential steps that directly influence the repair’s effectiveness and longevity.
Repairing Different Types of Damage
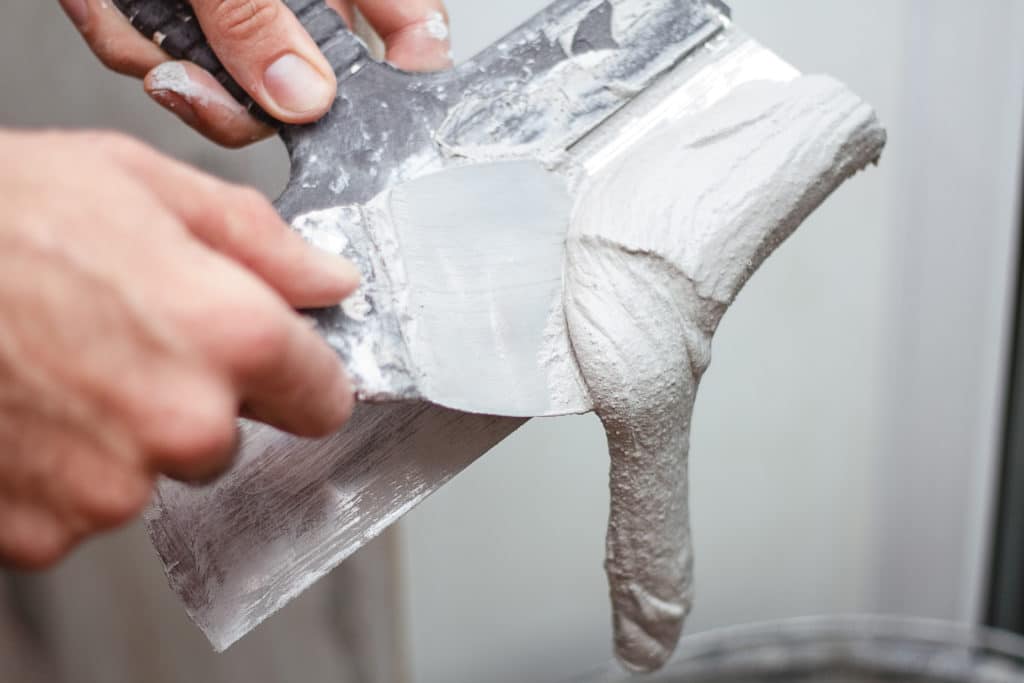
Proper repair strategies differ greatly depending on the severity and location of the concrete damage. Identifying the type of damage is critical for selecting the right repair material and method that will ensure the structural integrity and longevity of the concrete.
Addressing Small Cracks and Chips
Small cracks and chips in concrete can be effectively treated using a concrete patching compound that is suitable for the specific requirements of the job. These products are designed to bond well with existing concrete, providing a durable solution for minor imperfections.
- For Small Cracks:
- Best Concrete Patch: A vinyl-reinforced patching compound is commonly recommended to fix cracks in horizontal surfaces.
- Application: The area should be cleaned thoroughly before the compound is applied to ensure good adhesion.
- For Chips:
- Surface Preparation: Remove all loose material and clean the chipped area.
- Patch Application: Apply the patching compound tightly into the chipped area, ensuring it is level with the surrounding surface.
Handling Large Cracks and Holes
When dealing with larger damage, such as significant cracks or holes, the repair process becomes more complex and often requires different materials and tools.
- For Large Cracks:
- Expansion Joint: Pay special attention to cracks that may have formed around joints. They may need to be resealed to maintain the concrete slabs’ flexibility.
- Vertical Surfaces: Epoxy or a structural repair mortar can be used to fix cracks on vertical surfaces, ensuring proper bonding and support.
- For Holes:
- Structural Integrity: Evaluate the surrounding concrete to ensure that the patch will restore the structural integrity.
- Repair Material: Choose a repair mortar that sets quickly and is designed for larger repairs.
Note: When repairing either small or large damaged areas, curing times, weather conditions, and traffic loads must be considered to achieve optimal results.
Curing and Finishing for Long-Lasting Repairs
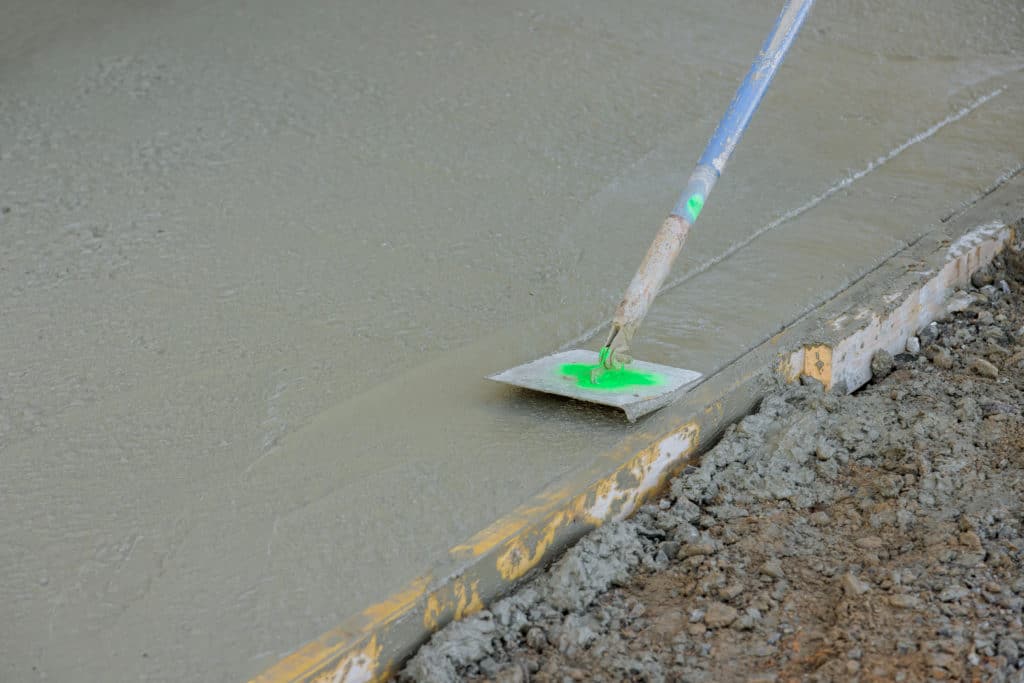
Achieving long-lasting concrete repair often hinges on the proper curing time and finishing methods. This section will articulate why these aspects are crucial and explore methods such as resurfacing and painting over to ensure durability and aesthetic appeal.
The Importance of Proper Curing Time
The process of curing is paramount for concrete to reach its maximum strength, which directly translates into the durability and longevity of the repair. Cure time should typically extend over several days and be carefully monitored, especially in fluctuating weather conditions which can affect the process. For example, a driveway repair might require varying timeframes for curing based on thickness and material specifications. Overlooking the significance of cure time can compromise the repair’s structural integrity.
- Recommendation: Allow at least 24 hours for light foot traffic and up to a week for vehicular traffic on driveway repairs.
- Consideration: Keep the patched area moist for a minimum of 7 days, given that proper water content is critical during the curing stage.
Options for Resurfacing and Painting Over
Once the concrete has adequately cured, one may consider resurfacing and painting over for a seamless and rejuvenated appearance. Resurfacing offers a fresh layer that can provide additional coverage and exceptional durability for tired, old concrete. It is critical to select a resurfacing product appropriate to the existing concrete’s condition and to abide by the manufacturer’s recommended application thickness.
- Paint over options are numerous, but an essential factor is the compatibility of the paint with the concrete material and environmental conditions. For instance, a breathable, weather-resistant paint is advisable for a concrete driveway.
- Attention: Ensure the concrete is properly cleaned and primed before resurfacing or painting to guarantee adhesion and longevity of the repair.
Implementing well-informed practices in curing and finishing can vastly enhance the life span of a concrete repair, ensuring it remains robust and visually pleasing for years.
Maintenance and Prevention Strategies
The longevity and structural integrity of concrete pavements hinge upon rigorous maintenance and proactive prevention measures. Implementing comprehensive strategies ensures enduring durability and optimal performance.
Regular Inspection and Maintenance Routines
Regular inspections are crucial in identifying and addressing minor issues before they escalate into significant problems. Maintenance routines should include:
- Visual Inspections: Routinely check for cracks, spalling, and drainage issues.
- Cleaning: Keep the surface clean to prevent the accumulation of materials that could cause damage.
Concrete maintenance must encompass timely repairs to reinforcing steel, which is vital to maintain the structural support it provides. Any signs of corrosion should be addressed immediately to prevent further degradation.
Preventative Measures for Concrete Longevity
Preventative measures extend the durability of concrete pavements. Important steps include:
- Sealing Cracks: Applying sealants to prevent water ingress and protect reinforcing steel.
- Applying Protective Coatings: Utilize coatings to guard against weathering, chemicals, and abrasion.
For continued guidance and assistance, contact us for up-to-date techniques and best practices that preserve concrete pavement effectively. Their expertise in preventative strategies serves as an invaluable resource for ensuring the lasting health of concrete structures.