Concrete surface grinding is a process utilized in the construction and remodeling of buildings, essential for preparing concrete surfaces for various finishes or treatments. Grinding concrete helps eliminate surface irregularities, including paint, adhesives, and imperfections, which often occur over time or during the concrete laying process. Professionals often use concrete grinders, machines with horizontally rotating discs embedded with abrasives, to level, smooth, or clean the surface of the concrete.
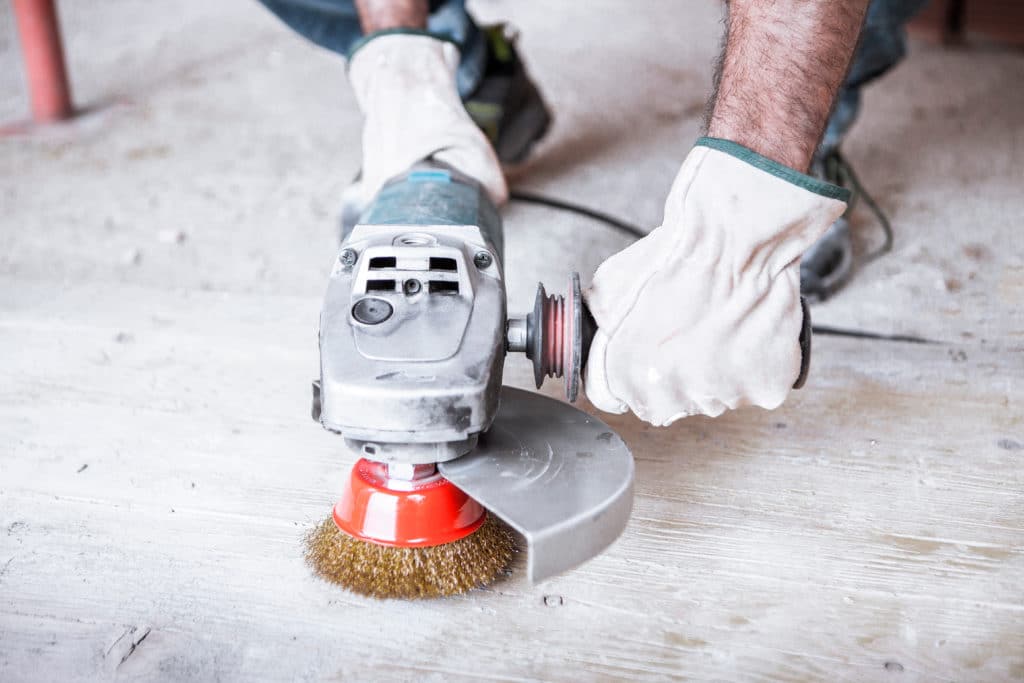
Understanding the tools and techniques for effective concrete grinding can be key to a successful flooring project. Different types of grinding attachments and grit levels allow for a range of finishes, from light texturing to opening the pores of the concrete, crucial for subsequent material applications. The technique can be employed for several applications, such as flattening high spots or ridges before flooring is installed, or for tapering cracks to reduce tripping hazards.
Proper surface preparation using grinding ensures that flooring or coatings adhere well to the concrete, increasing the longevity and performance of the surface. Whether dealing with pitted or stained concrete, grinding equipment available at rental centers simplifies the process, ensuring contractors can effectively prepare the concrete surface for their project needs.
Fundamentals of Concrete Grinding
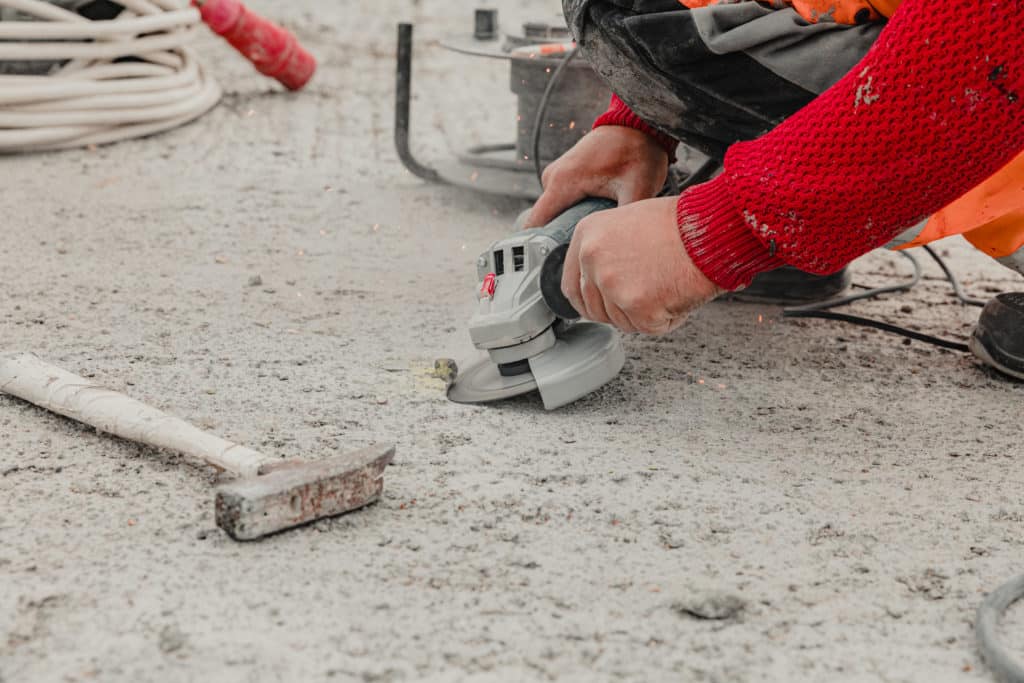
Concrete grinding is an essential process that involves refining the top layer of concrete to achieve a smooth and even surface. Appropriate for both new and existing floors, it demands precision and knowledge of the machinery and abrasives involved.
Understanding Concrete Grinding
Concrete grinding refers to the process where machines equipped with diamond grinding wheels abrade the surface of concrete to level, smooth, or clean it. It’s commonly used to remove imperfections, prepare surfaces for coatings, and correct concrete slab issues such as unevenness.
Types of Concrete Grinders
There are several types of concrete grinders, each suited for different tasks. Single-head grinders provide fine control for detailed work, while multi-disc grinders are more efficient on large surfaces. Handheld models address tight spaces and corners, and some grinders come with dust extraction features to maintain a clean work environment.
Selecting the Right Abrasives
Choosing the appropriate abrasives is crucial for effective concrete grinding. Diamond grains, varying in size and bond strength, are embedded into grinding wheels or discs. Harder diamond abrasives are necessary for softer concrete, while softer diamonds are better for harder concrete surfaces. The coarseness of the abrasive impacts the finish and is selected based on the required surface texture.
Surface Preparation Techniques
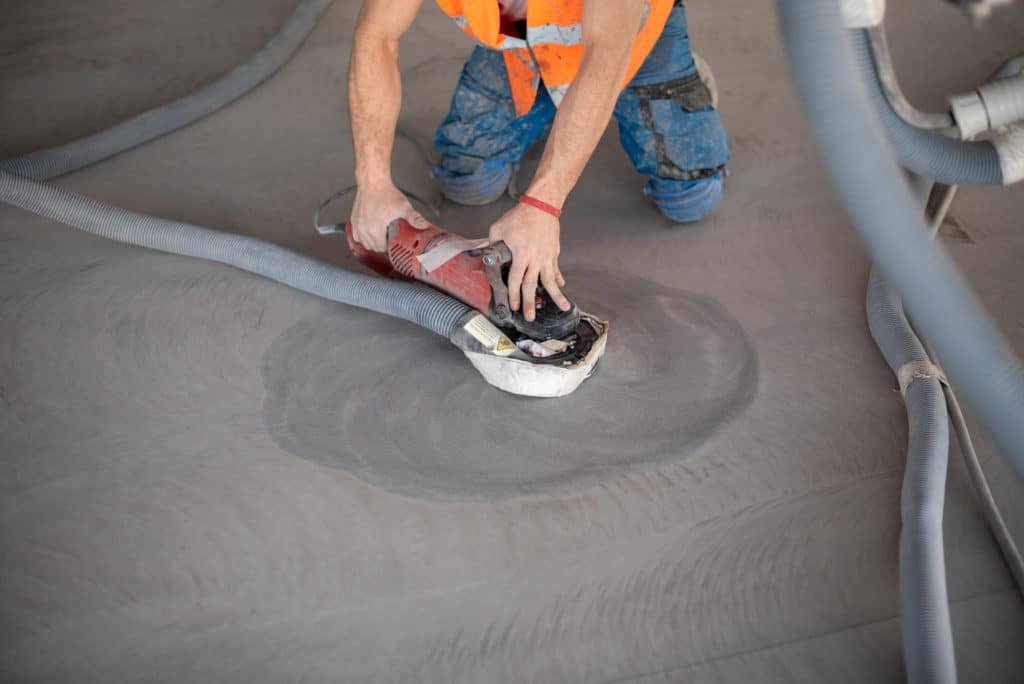
Before applying a new coating or overlay, a crucial step is to properly prepare the concrete surface. This ensures that the new material adheres well and lasts longer, providing a high-quality finish.
Assessing the Concrete Surface
The initial phase in surface preparation involves a detailed inspection of the concrete. Professionals need to identify uneven concrete surfaces, high spots, and any presence of adhesives, coatings, glue, or mastics. These irregularities must be addressed to achieve a sufficiently smooth base for subsequent treatments. State-of-the-art surface preparation equipment is required to properly assess and prepare the surface.
Cleaning and Clearing the Area
From the start, the area must be cleaned thoroughly. This includes removing dust, debris, and any loose or flaking material from the surface. An effective cleaning ensures that nothing interferes with the grinding process. Employing methods such as shot blasting and using diamond grinders can remove old adhesives and coatings, and prepare the surface for new applications. Environmental and safety measures are taken during this process to protect workers and ensure compliance with regulations.
Grinding Process and Operations
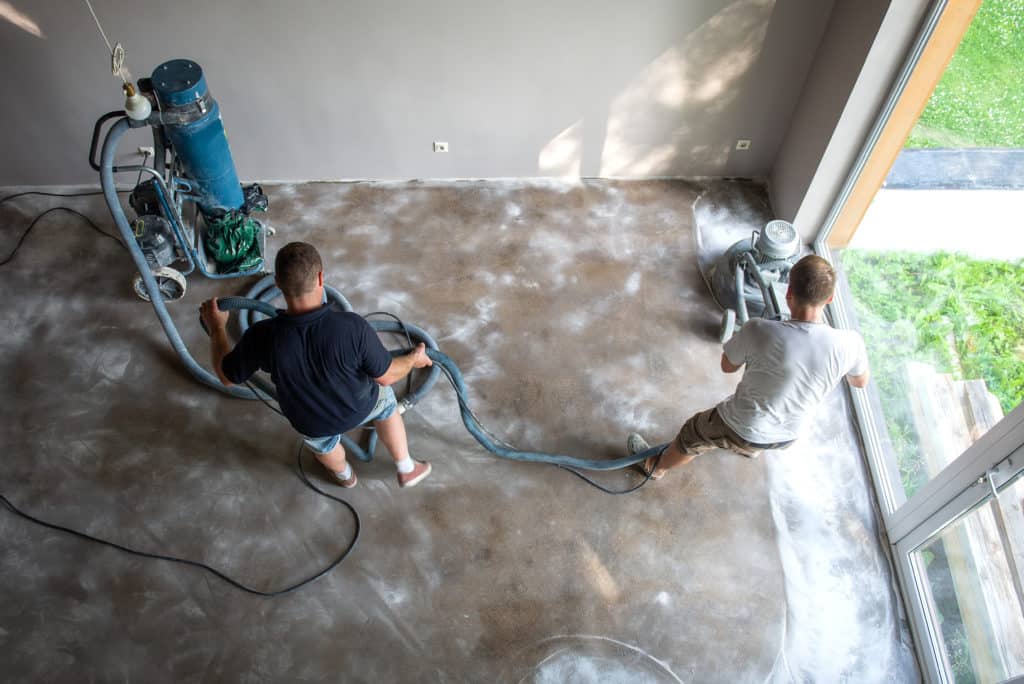
Concrete surface grinding is a precise operation that requires an understanding of the machinery and the desired finish. Proper technique and equipment management are crucial to achieving a smooth, level surface.
Operating Concrete Grinders
Operating concrete grinders involves guiding the floor grinder or handheld grinders across the concrete surface. The operator adjusts the speed of the rotating discs fitted with abrasive grits to remove the material at a consistent rate. These discs can be made of industrial-grade diamonds, tungsten carbide, or steel, each suited for different levels of grinding. The steps typically start with a coarser grit for initial material removal and transition to finer grits for smoothing and eventual polishing.
It’s important to replace the discs at the right intervals to maintain efficiency and surface quality. Maintenance of the grinders also plays a critical role, ensuring longevity and safety of the machinery.
Managing Grinding Residue
During the grinding process, operators must effectively manage the grinding residue—consisting primarily of dust and concrete particles. Adequate dust collection systems are essential to maintain a clean working environment and to comply with safety regulations.
For certain applications, especially indoor settings, a method to cover the surrounding areas and mitigate dust spread is necessary. Additionally, some operations may involve wet grinding, which introduces water into the process to help control dust and cool the grinding discs, adding an extra layer of complexity to the residue management.
Safety and Maintenance
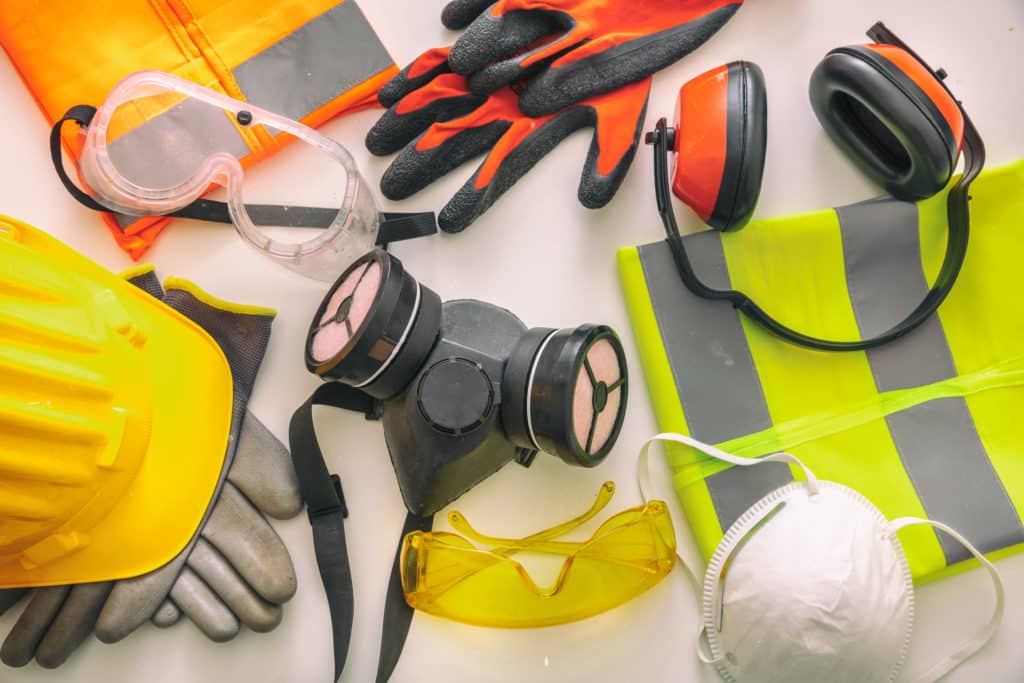
Ensuring the safety of operators and maintaining the condition of concrete grinders are critical components to any concrete grinding project. Personal protective equipment is essential to shield the user from harm, while regular maintenance ensures the longevity and effectiveness of the equipment.
Personal Protective Equipment
The use of personal protective equipment (PPE) is imperative to safeguard workers from various hazards during concrete grinding. Workers should wear:
- Safety glasses or goggles to protect the eyes from flying particles.
- A respirator or dust mask to prevent inhalation of harmful dust particles.
- Hearing protection, such as earplugs or earmuffs, to shield the ears from loud noise produced by the machinery.
- Gloves to protect the hands and improve grip on the equipment.
- A face shield to offer additional face protection from debris.
Grinder Maintenance and Upkeep
Regular maintenance and upkeep of concrete grinders are crucial to efficient operation and the prevention of costly repairs. Proper maintenance includes:
- Cleaning the machine after each use to remove concrete dust and buildup.
- Inspecting all components, including the integrity of safety gear.
- Ensuring effective dust control by checking the vacuum attachment and filters are clean and working properly.
- Tightening loose screws and replacing worn parts to maximize performance and safety.
Advanced Techniques and Finishing
When refining concrete surfaces, advanced techniques such as concrete polishing and specialized grinding applications are crucial for achieving a professionally finished look. The precise selection of tools and methods is fundamental to the success of the project, ensuring a surface that is not only aesthetically pleasing but also meets functional standards.
Concrete Polishing
Concrete polishing transforms a rough surface into a glossy and smooth finish, enhancing both its durability and appearance. This is achieved through the use of finely gritted polishing pads and planetary grinders, which are designed to orbit horizontally rotating discs to grind and polish floors with great precision. The process often follows a sequence, starting with coarse grinding with diamond tools and progressing to finer grits for a polished finish. Whether utilizing a wet or dry vacuum system, controlling dust is a key concern during polishing to maintain a clean work environment and to prevent contamination of the finished surface.
- Tools & Materials:
- Planetary grinders
- Diamond tools
- Polishing pads
- Wet/dry vacuum
- Process:
- Start with coarse grinding
- Gradually move to fine grinding
- Finish with very fine polishing grit
Specialized Applications for Grinding
Specialized applications for grinding tackle complex challenges such as concrete repair and coating removal. For instance, removing old coatings or adhesives from a concrete substrate requires robust equipment such as grinders equipped with a special matrix of diamond segments. This matrix is designed to cut through tough materials and can be adjusted to cater to different types and thicknesses of coatings. During coating removal, it is important to work methodically to avoid damaging the existing concrete structure while ensuring complete removal of the unwanted substance.
- Challenges:
- Concrete repair
- Coating removal
- Solutions:
- Use specialized diamond matrix tools
- Apply systematic grinding techniques
To ensure precision and efficiency in these advanced techniques and applications, operators must select appropriate machinery and accessories—each choice plays a pivotal role in achieving the desired outcome of a well-executed concrete grinding and finishing project.