Concrete tanks serve a critical role in municipal and industrial facilities, particularly for water and wastewater infrastructure. However, like all constructed facilities, these tanks are prone to deterioration over time due to factors such as environmental stress, corrosion, and structural loading. The need for inspection, rehabilitation, and retrofit services increases as these structures age. With appropriate concrete tank repair strategies, communities and industries can extend the service life of these tanks, ensuring continued functionality and safety.
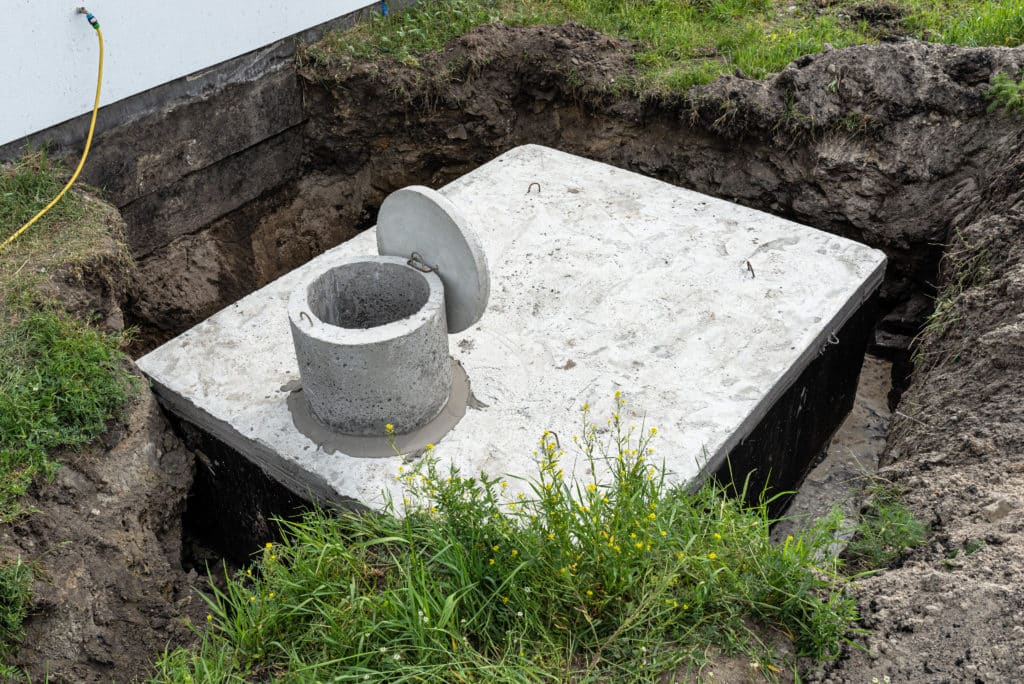
The process of concrete tank repair involves various techniques and considerations. It focuses on evaluating the current condition of the tank, identifying the root causes of damage, and applying the most effective repair methods. From addressing cracks and leaks to reinforcing structural integrity, repair work is tailored to the specific issues and requirements of each tank. Skilled professionals can employ advanced materials, such as fiber-reinforced polymers, and apply them from both the positive or negative side of hydrostatic pressure, depending on the situation.
Rehabilitating concrete tanks can be a cost-effective alternative to replacing them entirely. It preserves the existing infrastructure while improving performance and resilience. Moreover, proper repairs are essential for tanks holding drinking water, as they must be compliant with safety and health regulations. In such cases, specific food-grade materials and liners are used to maintain the quality of the water stored. The significance of high-quality repair work cannot be overstated, as it directly impacts the reliability of water supply and waste management systems.
Inspection and Diagnosis
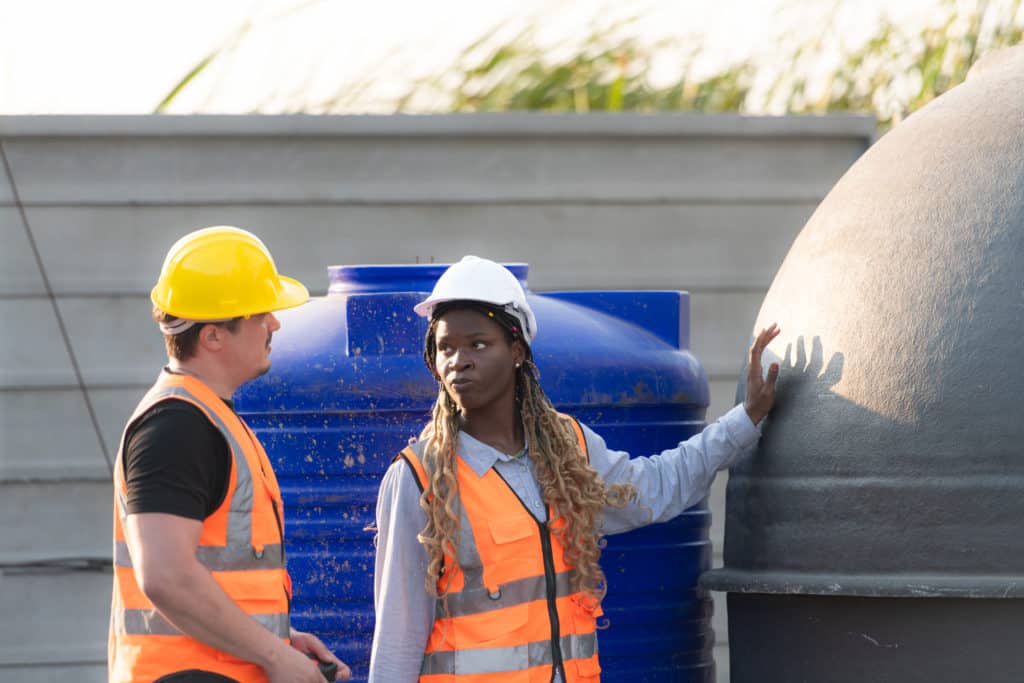
Before initiating any repair work on concrete tanks, a thorough inspection and diagnosis are imperative. This process ensures that the repair strategy addresses all relevant safety and structural concerns, leading to durable and effective maintenance solutions.
Concrete Tank Evaluation
To begin, one should conduct a detailed evaluation of the concrete tank. It involves a close examination of the tank’s surface conditions, including any visible signs of deterioration such as spalling or efflorescence. They must document all areas with apparent damage or wear, as this will guide subsequent steps in the inspection process.
Leak Detection and Analysis
Following initial assessment, leak detection and analysis become pivotal. Professionals use a combination of visual inspections and advanced technology like acoustic emission testing to locate and determine the leaks’ sources. This step is crucial to identifying potential safety hazards and preventing water loss, which can be especially critical in sustaining infrastructure.
Structural Integrity Assessment
Finally, assessing the structural integrity of concrete tanks involves checking for cracks and other signs of structural failure. Engineers typically utilize non-destructive testing methods such as ultrasound and radiography to collect data on the tank’s condition without causing further damage. This assessment is vital to ascertain the tank’s ability to continue safe operation within design specifications.
Concrete Tank Repair Techniques
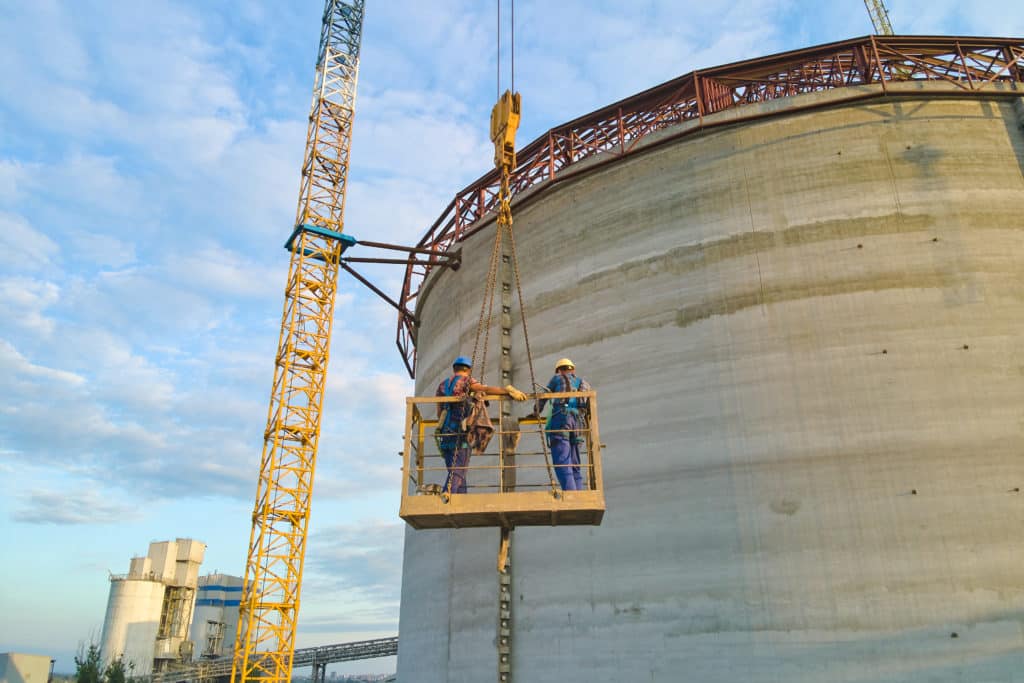
When addressing the integrity of concrete tanks, various repair techniques are implemented to restore structural strength and durability. Specialized methods target specific damage types such as cracks, surface spalling, and more extensive deterioration. In employing these techniques, professionals aim to extend the tank’s service life and ensure its safe use for water storage or treatment.
Crack Repair Methods
For minor to moderate concrete tank crack repairs, epoxy or polyurethane resins are often injected under pressure to fill and seal the cracks. Epoxy injections offer a strong, rigid repair that bonds the cracked sections and restores the concrete’s original strength. Alternatively, polyurethane foam injections are used for their flexibility and water resistance, which can accommodate slight concrete movements and stop water leaks.
- Apply sealant: Surface preparation is crucial; it should be clean and free from debris.
- Inject resin: Utilize specialized tools to inject epoxy or polyurethane into the cracks.
Surface Spalling and Delamination
Spalling and delamination indicate surface layer deterioration, often requiring repairs like shotcrete application or hand-applied mortar.
- Surface Preparation: Remove loose concrete and contaminants to achieve a clean surface.
- Application: Use shotcrete or hand-applied mortar for the repair site; ensure compatibility with the existing concrete.
This method revives the structural surface and precludes further damage, effectively enhancing the tank’s durability.
Full-Depth Repair and Rehabilitation
When concrete tanks suffer from extensive damage, full-depth repair and rehabilitation are necessary. Such a process might involve the removal of deteriorated concrete sections and the replacement with new concrete, often enhanced with waterproofing agents.
- Removal: Excavate damaged concrete fully to expose the sound substrate.
- Replacement: Deploy form-and-pour techniques or shotcrete for larger areas.
Proper curing practices are integral to ensure the longevity of the repair. Post-repair, a waterproofing layer is sometimes added to protect against future ingress and degradation.
Materials and Tools for Concrete Tank Repair
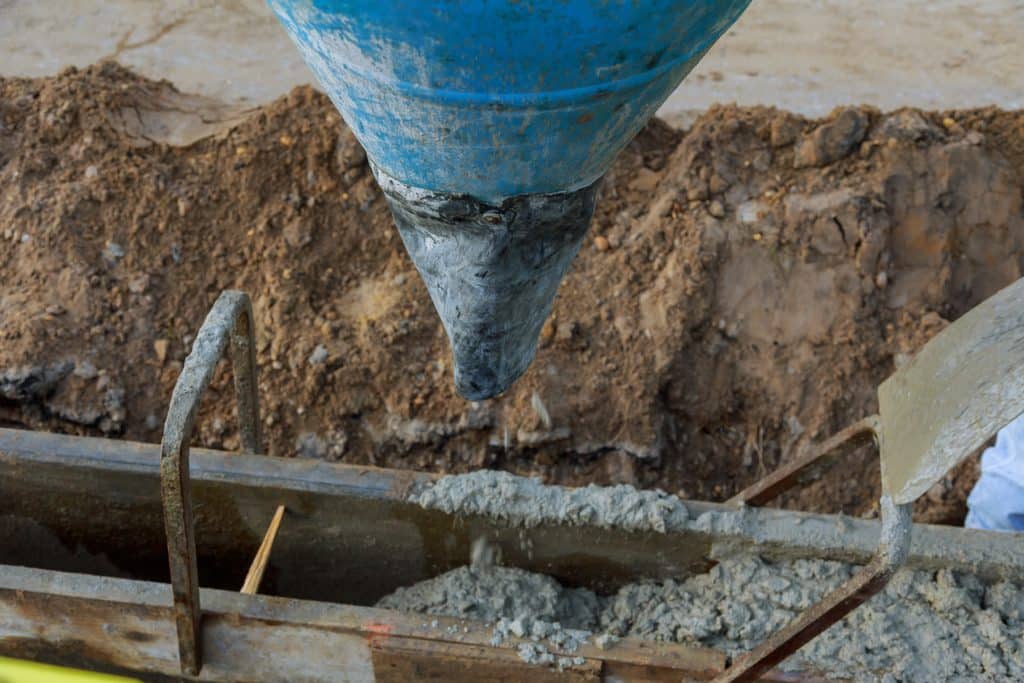
Concrete tank repair is integral to maintaining the structural integrity and functionality of the system. Effective repairs rely on high-quality materials and precise tools, ensuring a long-lasting solution to leakage or deterioration.
Repair Mortars and Hydraulic Cement
For addressing cracks and structural damage in concrete tanks, specialized repair mortars and hydraulic cement are essential. Repair mortars provide strong adhesion and durability, with some products like Krystol repair grout effectively sealing against water penetration. Hydraulic cement is beneficial due to its quick-setting properties and ability to halt active water leaks.
- Cement: Standard cement is not suited for repair; instead, a specialized repair mortar should be used.
- Hydraulic Cement: Offers rapid setting and is suitable for stopping water flow in active leaks.
Reinforcement and Bonding Agents
Strong repairs require not only the right filler materials but also enhancements to the existing structure. Steel reinforcement may be integrated to fortify the repair. To bond the new material to the old concrete, a concrete bonding agent must be applied, promoting adhesion and preventing issues like rust on steel reinforcements.
- Steel: Mesh or rebar for structural reinforcement, preventing further cracking.
- Concrete Bonding Agent: Ensures a secure bond between new and old concrete surfaces.
Sealers and Waterproofing Materials
The final steps in concrete tank repair involve sealers and waterproofing agents to protect against future water infiltration. Epoxy and adhesive sealants provide a resilient and impermeable layer over repaired areas. Consider sealers for waterproofing your concrete tanks to guard against further water damage and corrosion.
- Epoxy: Creates a hard, impermeable surface over the repaired areas.
- Adhesive: Additional option as a sealer to further secure the repair.
By carefully selecting and applying these materials and tools, concrete water tanks can be effectively restored, ensuring their ongoing performance and longevity.
Maintenance and Prevention
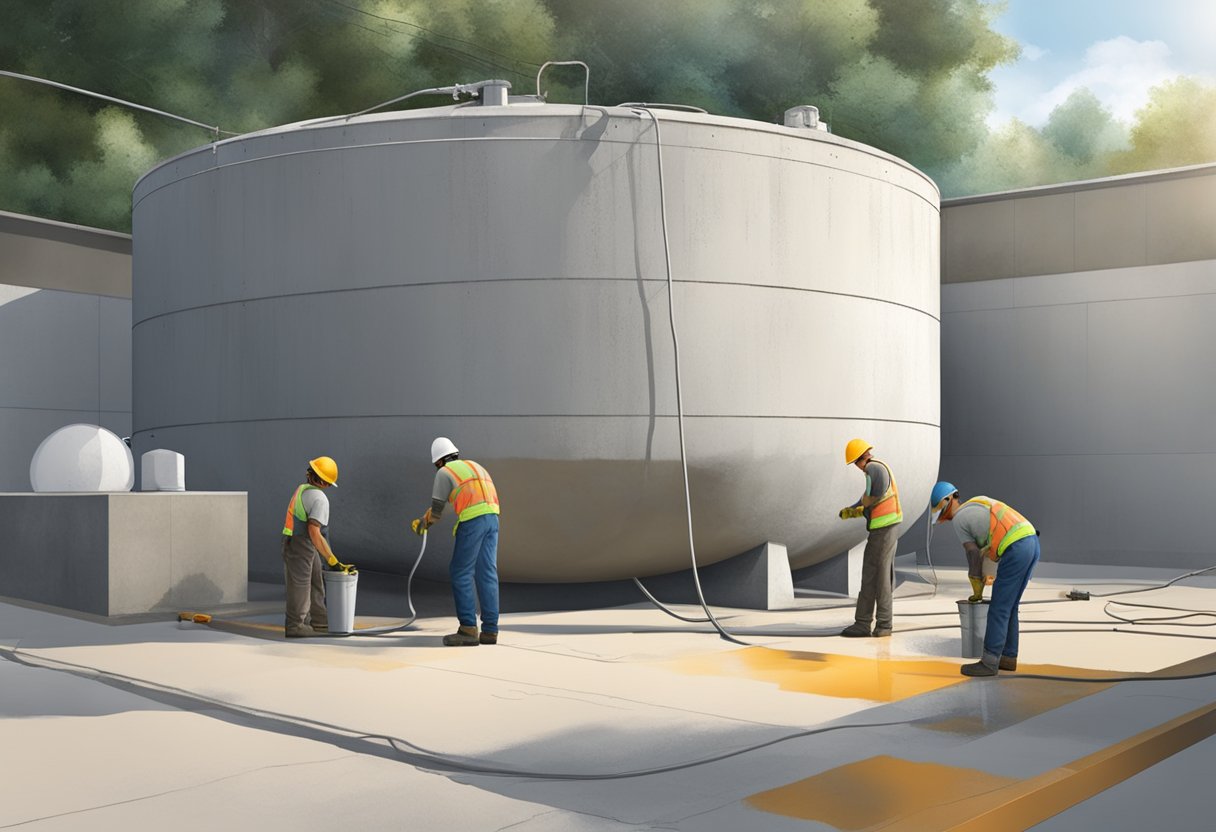
Maintaining and preventing issues in concrete tanks are essential to ensure water safety and the longevity of the infrastructure. A consistent schedule for routine tank maintenance and leak prevention strategies is critical, as is planning for long-term infrastructure care.
Routine Tank Maintenance
Tank maintenance is not just about cleanliness; it is also crucial for the operational integrity of water storage systems. They should regularly inspect the interior and exterior of the tank for any signs of wear, deterioration, or leakage. It is important to:
- Inspect: Perform detailed inspections bi-annually to identify any potential issues.
- Clean: Schedule regular cleaning to remove sediments and prevent contamination.
Leak Prevention Strategies
To prevent leaks, concrete tanks require robust strategies that include the use of secondary containment measures and leak detection systems. Some preventative measures include:
- Applying waterproof coatings to protect against water infiltration.
- Installing sensors and alarms for early leak detection.
Long-term Infrastructure Care
Investing in long-term care ensures the safety and functionality of concrete tanks. This involves:
- Assessing and upgrading older tanks with modern materials and techniques.
- Implementing a proactive maintenance schedule that includes periodic safety checks and repairs.
By adhering to these maintenance and prevention strategies, the service life of concrete tanks can be significantly extended, offering reliable performance and safeguarding water quality.
Regulations and Standards
When addressing repairs for concrete water tanks, adherence to specific regulations and standards ensures safety and longevity of the structures. Two main points of reference include the American Water Works Association (AWWA) standards and relevant building codes that dictate concrete tank specifications.
AWWA Standards for Water Tanks
The AWWA provides comprehensive guidelines that engineers must follow when inspecting and repairing water storage tanks. AWWA standards, namely AWWA D110 and D115, specify the design, construction, and maintenance protocols for concrete tanks, including permissible leakage rates. These standards are essential for maintaining tanks in a safe operational state and preventing water contamination.
Building Codes and Concrete Tank Specifications
Building codes play a pivotal role in defining the specifications for concrete tank repairs. These codes ensure that the tanks meet the structural and safety requirements necessary to withstand environmental stresses and usage demands. Engineers are responsible for ensuring repairs align with both local building codes and industry standards, which collectively ensure the integrity and safety of concrete water storage tanks.